Looking Good Tips About How To Convert Torque Into Tension
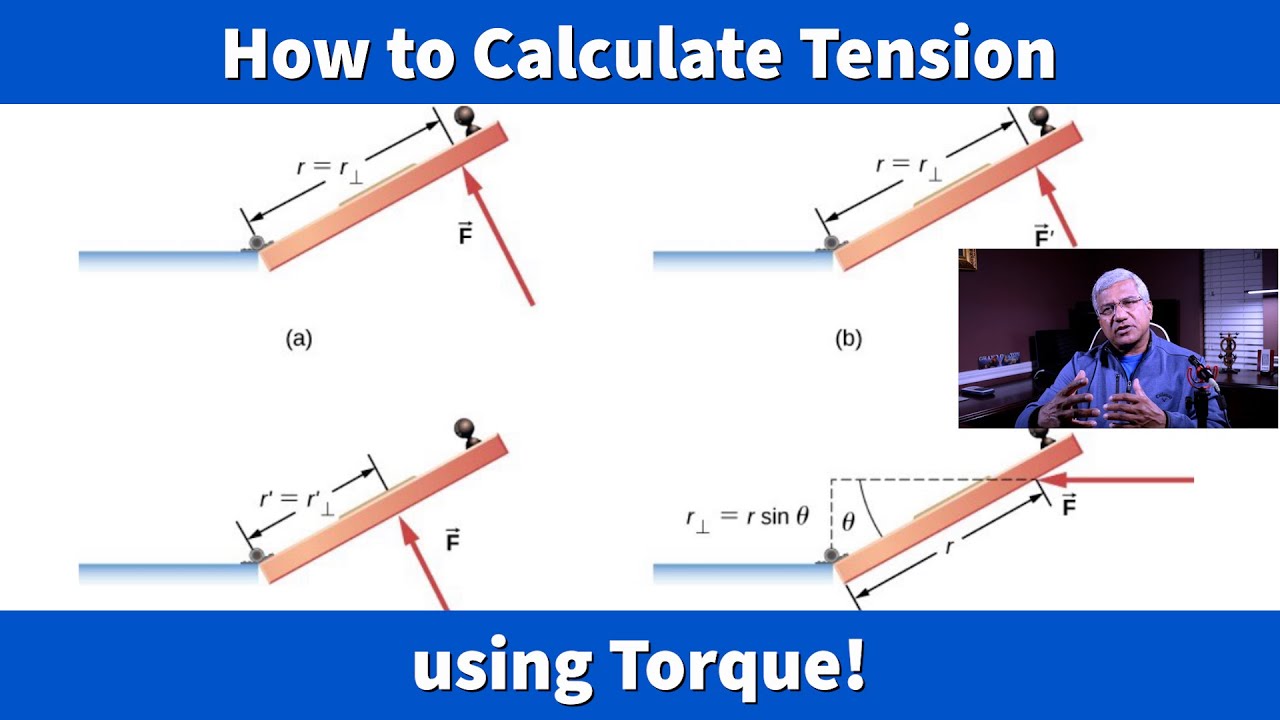
Calculating Tension Using Torque An Important Example Explained YouTube
Understanding Torque and Tension
1. What Exactly Are We Talking About?
Let's get something straight right off the bat: torque and tension, while related, are not the same thing. Think of torque as a twisting force — imagine tightening a bolt with a wrench. You're applying torque. Tension, on the other hand, is a pulling force — picture a rope being stretched taut. That's tension in action.
The relationship between the two often shows up when you're trying to achieve a specific clamping force with bolted connections. You apply torque to tighten the bolt, and that torque creates tension in the bolt itself, which in turn clamps the parts together. It's a beautiful, albeit sometimes complicated, dance of forces.
Why bother converting one to the other? Well, in many engineering applications, you care more about the tension (the clamping force) than the torque applied. Knowing the tension ensures the joint is secure and won't loosen under stress. Torque is simply the tool we use to get to the desired tension. It's the means to an end, so to speak. It is important to understand the relation between these two element. Torque can affect the tension of an object.
It is important to note that there are many tool to measure these element. From a simple torque wrench, up to load cell to see the tension in the cable. There are also method that is not related to calculation, such as visually inspect the tension of the cable or the condition of bolts.

Force And Torque Measurements Vrogue.co
The Formula
2. The Bolt Tightening Equation
Ready to get a little mathematical? The core formula that links torque and tension for bolted connections is: T = K D P. Don't run away screaming! Let's break it down.
In this equation:
- T represents the torque applied (usually measured in lb-ft or Nm).
- K is the "nut factor" or "torque coefficient" (a dimensionless value, usually between 0.10 and 0.20). This accounts for friction between the bolt, nut, and the clamped surfaces.
- D is the nominal bolt diameter (in inches or millimeters).
- P is the axial tension in the bolt (the clamping force, usually measured in pounds or Newtons).
Essentially, this formula tells us that the torque required to achieve a certain tension is proportional to the bolt diameter and the nut factor. A bigger bolt or a higher friction coefficient will require more torque for the same tension. And, naturally, a higher tension will require more torque. This is why choosing the right tools are important.
It's worth remembering that this formula is an approximation. Real-world conditions can influence the relationship. Things like surface finish, lubrication, and even the tightening speed can affect the actual tension achieved for a given torque. Use it as a starting point, but always verify your results if accuracy is crucial.
Factors That Mess With the Conversion
3. Friction, Lubrication, and More
Ah, friction, that ever-present troublemaker! The nut factor (K) in the formula is all about friction. It's the biggest variable and the most significant source of error. The friction between the threads of the bolt and nut, as well as the friction under the nut face, dramatically affects how much of your applied torque actually translates into tension.
Lubrication is your friend here! Applying a lubricant (like anti-seize compound) reduces friction, leading to a lower nut factor. This means you'll achieve a higher tension for the same applied torque. Just be sure to use a lubricant that's compatible with the materials involved and that you know the lubricant's effect on the nut factor.
Other factors to consider are the surface finish of the mating parts, the tightening speed (slow and steady wins the race, preventing galling and inconsistent friction), and even the temperature. Everything can affect the torque-tension relationship, making precise conversions a bit of an art as well as a science. Not to mention the proper torque wrench.
Another critical factor is the condition of the threads. Damaged or corroded threads will significantly increase friction and make the torque-tension relationship unpredictable. Always inspect bolts and nuts before use and replace any that are questionable. After all, a little preventative maintenance goes a long way, and keeps you safe.
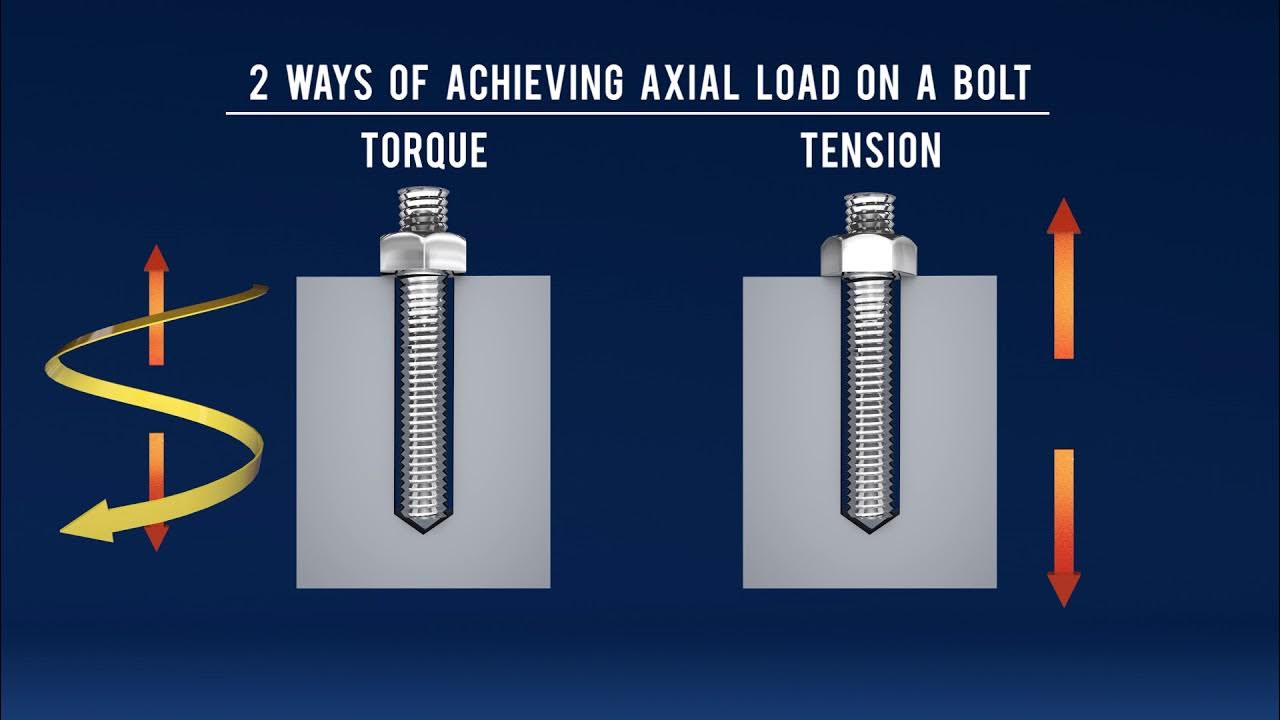
Bolt Tensioning Vs. Torquing, Compared YouTube
Practical Tips for Accurate Conversions
4. Getting the Best Results
So, how do you put all this knowledge into practice and get reliable torque-to-tension conversions? First, always use a calibrated torque wrench! This is non-negotiable. A cheap, inaccurate wrench is worse than no wrench at all. Make sure your wrench is appropriate for the torque range you're working with and that it's been recently calibrated.
Second, research the recommended torque values for your specific application. Bolt manufacturers and engineering standards often provide torque specifications that take into account the bolt size, material, and intended use. These values are usually based on extensive testing and are a good starting point.
Third, consider using a torque-tension analyzer. These devices directly measure the tension in the bolt as you apply torque, allowing you to fine-tune your process and verify that you're achieving the desired clamping force. They're more expensive than a torque wrench, but they provide invaluable data for critical applications. You can also use a load cell, depending on the condition
Finally, don't be afraid to experiment and document your results. Torque-tension relationships can vary depending on the specific circumstances, so it's always a good idea to perform some tests to validate your assumptions and refine your tightening procedures. Good data is always important. Keep records!
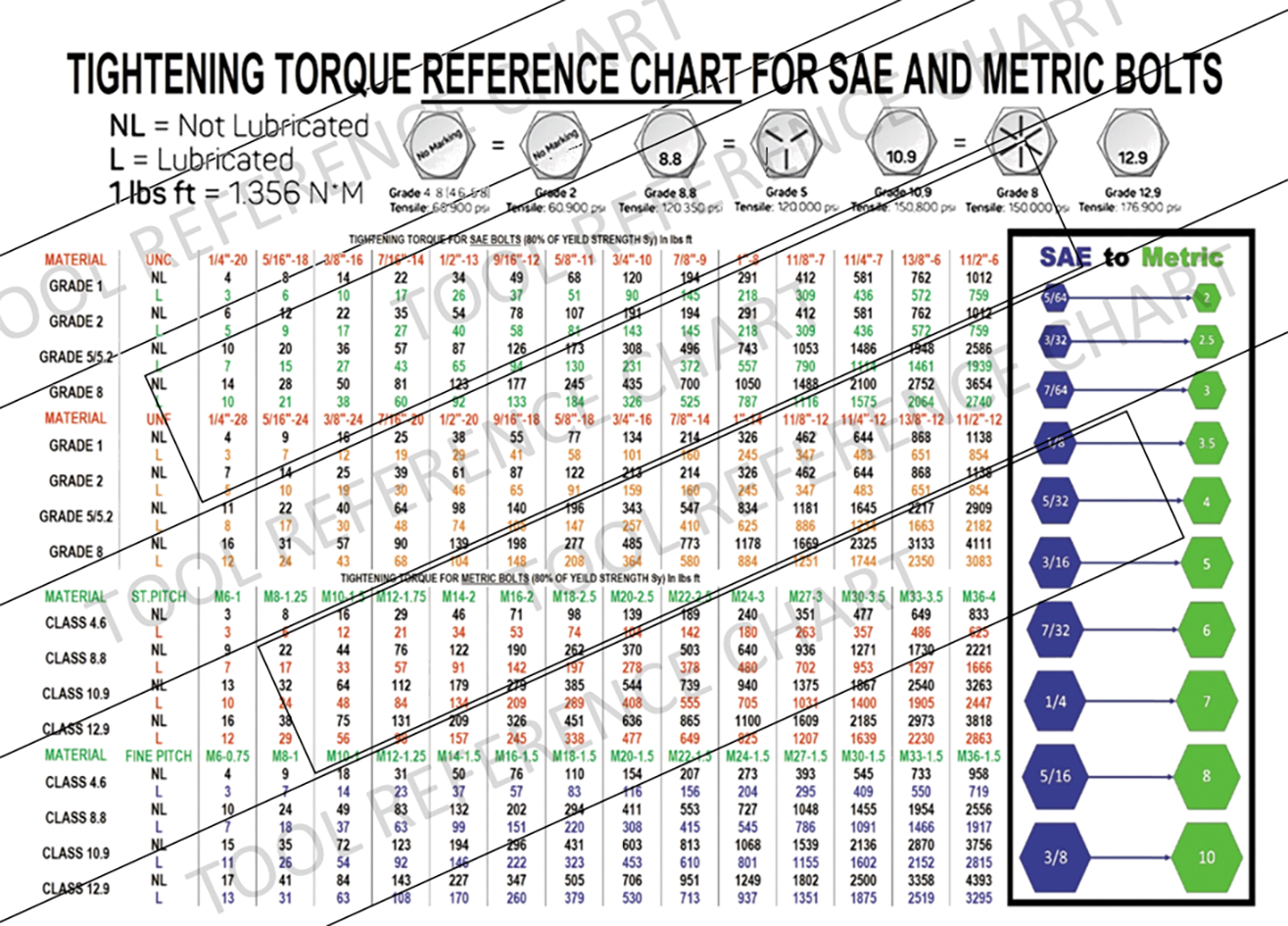
Torque Tightening Chart SAE & Metric Bolt Conversions Wrench
Beyond the Basics
5. Torque Angle Tightening and More
For highly critical applications, consider using torque-angle tightening methods. This involves tightening the bolt to a snug fit using a torque wrench and then rotating the bolt a specified number of degrees. This technique helps to overcome variations in friction and achieve a more consistent tension. It is a good practice, and often is overlooked.
Ultrasonic extensometers can also be used to measure bolt stretch directly. These devices send ultrasonic waves through the bolt and measure the change in length as it's tightened. This provides a very accurate measurement of the tension in the bolt, regardless of friction or other variables. This is especially useful to see the condition of the material.
Finite element analysis (FEA) can be used to model the torque-tension relationship and predict the tension achieved for a given torque under various conditions. FEA is a powerful tool for optimizing bolted connections and ensuring that they meet the required performance criteria. And if you can do that, it saves you a lot of time.
Remember, understanding how to convert torque into tension is about more than just plugging numbers into a formula. It's about understanding the underlying principles, considering the various factors that can affect the relationship, and using appropriate tools and techniques to achieve the desired results. Now you know why this is so important.
