Simple Info About How To Read Dial Gauge 0.01 Mm

Unlocking the Secrets of the 0.01 mm Dial Gauge
1. Understanding the Basics
Ever wondered how machinists and engineers achieve such incredible precision? The secret often lies in seemingly simple tools, like the dial gauge. But a dial gauge that reads to 0.01 mm? That's serious business! This isn't about eyeballing it; it's about consistent, reliable measurements that can make or break a project. Think of it like this: if you're building a delicate clock, a tiny fraction of a millimeter can throw the whole thing off. Thats where this nifty instrument comes into play, providing the accuracy you desperately need.
The real beauty of a dial gauge, especially one calibrated to 0.01 mm, is its ability to detect minute variations. Were talking about movements so slight you wouldnt even notice them with the naked eye. This level of sensitivity is essential in many fields, from manufacturing to quality control. Imagine checking the flatness of a surface or the runout of a rotating shaft. Without this level of precision, you're just guessing, and guessing is rarely a winning strategy when accuracy is crucial.
So, why 0.01 mm? Well, it represents a significant step up in accuracy from standard gauges. This level of detail lets you catch imperfections and ensure that parts are within very tight tolerances. Its about eliminating guesswork and having confidence in your measurements. After all, who wants to spend hours crafting something only to find out its slightly off because of a minor measurement error?
Before you can read a dial gauge to this level of precision, you need to grasp the fundamentals. We're talking about understanding the main components, how they work together, and the importance of proper setup. Don't worry, it's not rocket science, but a little preparation will go a long way. Think of it as learning a new language, but instead of verbs and nouns, youre dealing with pointers, scales, and revolutions. A journey into the world of very, very small measurements!

How To Measure With A Dial Indicator Correctly Klassik ATS
Deciphering the Dial
2. Reading the Main Scale
Alright, let's get our hands dirty! First things first, familiarize yourself with the main scale of the dial gauge. This is usually the larger, more prominent scale on the gauge face. Each division on this scale typically represents 0.01 mm, which is the unit of measurement we are interested in. So, every time the needle moves from one line to the next, that's a tiny 0.01 mm of movement.
To start reading, pay close attention to where the large needle is pointing. Each number on the main scale represents a certain number of hundredths of a millimeter. For example, if the needle is pointing directly at the number '5', that signifies a movement of 0.05 mm. Easy peasy, right? But don't get too comfortable; there's more to it than just staring at the big needle!
The tricky part sometimes is estimating the reading if the needle falls between two lines. Dont panic! Just try to visually divide the space between the lines and estimate the fraction of 0.01 mm. With a little practice, you'll become a pro at guesstimating those in-between values. However, remember that reading the smaller scale for precise measurements will give you the most accurate result.
Remember that the main scale is your foundation. It gives you the initial reading, the "ballpark" figure, if you will. Before moving to the finer details, make sure you understand what the main scale is telling you. Get comfortable with reading it accurately, and the rest will fall into place. It's like learning the alphabet before writing a novel; it's an essential stepping stone.
3. The Revolution Counter
Now, let's talk about the revolution counter, often a smaller dial within the main gauge face. This little helper keeps track of how many full revolutions the main needle has made. Why is this important? Because a single revolution on the main dial usually represents a whole millimeter of movement!
Think of the revolution counter as the "ones" place in a decimal system, while each tick on the main dial represents the "hundredths" place. Each number on the revolution counter indicates how many full millimeters the plunger has moved. So, if the revolution counter is pointing at the number '1', that means the main needle has completed one full revolution, and the plunger has moved 1 mm.
Here's a crucial tip: always read the revolution counter before you read the main scale. Knowing how many full millimeters the plunger has moved gives you a starting point for determining the total measurement. This will prevent you from making significant errors in your readings, especially when dealing with larger movements.
Ignoring the revolution counter is like forgetting to carry the one in a math problem. It can throw off your entire calculation. So, make sure to give it the attention it deserves. A quick glance at the revolution counter can save you from misinterpreting the reading on the main dial and ensure you're always on the right track. It's your reliable compass in the world of tiny measurements.

Dial Gauges Measurement Tools & Equipment MISUMI
Putting It All Together
4. Combining Main Scale and Revolution Counter Readings
Alright, you've mastered the individual components. Now it's time to combine your knowledge and calculate the final reading! This is where the magic happens, where all the individual pieces come together to reveal the precise measurement.
Here's the formula: Total Reading = (Revolution Counter Reading) + (Main Scale Reading). Let's break that down with an example. Imagine the revolution counter is pointing at '2', and the main needle is pointing at '35' on the main scale. That means the total reading is 2 mm + 0.35 mm = 2.35 mm. See? Not so scary after all!
But, the devil is in the details. Ensure you convert the main scale reading into millimeters by dividing it by 100. Remember, each division on the main scale represents 0.01 mm. So, a reading of '35' corresponds to 0.35 mm. Always double-check your conversions to avoid errors. It's easy to get tripped up if you're not careful.
Accuracy is paramount here. A slight misinterpretation of either the revolution counter or the main scale can lead to a significant error in your final reading. So, take your time, double-check your numbers, and practice regularly. With enough practice, this process will become second nature, and you'll be reading dial gauges like a seasoned pro. You'll be saying 'I can read dial gauge 0.01 mm' with no hesitation!
5. Accounting for Plus and Minus Signs
One last thing to consider: dial gauges can sometimes indicate movement in both positive and negative directions, depending on the setup and application. This is crucial because it tells you whether the measured object is larger or smaller than the reference point.
Often, the dial gauge is zeroed at a specific point. Any movement away from that point in one direction is considered positive, while movement in the opposite direction is negative. The gauge itself won't necessarily show a plus or minus sign, so it's up to you to interpret the reading correctly based on how the gauge is set up.
Consider this scenario: you're using a dial gauge to measure the variation in the diameter of a shaft. If the dial gauge reading is positive, it means that the diameter is larger than the initial diameter at which you zeroed the gauge. Conversely, if the reading is negative, the diameter is smaller.
Understanding the directional aspect of dial gauge readings is vital for making informed decisions about your measurements. Misinterpreting the direction can lead to incorrect assessments and potentially flawed outcomes. Always pay attention to how the dial gauge is set up and what each direction represents in the context of your measurement. A keen awareness of plus and minus signs is a hallmark of a skilled dial gauge reader!

Tips and Tricks for Accurate Readings
6. Zeroing the Gauge
Before you even think about taking a measurement, the most crucial step is properly zeroing the dial gauge. A poorly zeroed gauge will give you inaccurate readings every single time, rendering the whole process useless. Its like trying to weigh something on a scale that doesnt start at zero; the result will always be off.
Zeroing typically involves setting the dial gauge against a known reference surface and adjusting the dial until the needle points precisely to zero. This ensures that the gauge is calibrated to the correct starting point. Make sure the reference surface is clean and free of any debris that could affect the zeroing process. Even a tiny speck of dust can throw off your readings.
Different dial gauges may have slightly different zeroing mechanisms. Some have a rotating bezel that you can turn to align the needle with zero, while others might have a more sophisticated adjustment system. Refer to the manufacturer's instructions for your specific gauge model. Understanding the zeroing procedure is non-negotiable for accurate measurements.
Regularly check the zero setting throughout your measurement process. Vibrations, temperature changes, or even accidental bumps can cause the gauge to drift out of zero. Its a good habit to periodically re-zero the gauge to ensure that your readings remain consistent and reliable. Think of it as a quick tune-up to keep your measuring instrument in top condition.
7. Mounting and Stability
The way you mount the dial gauge significantly impacts the accuracy of your measurements. A wobbly or unstable setup can introduce vibrations and inconsistencies, leading to erroneous readings. Its like trying to take a steady photograph on a shaky tripod; the result will be blurry.
Ensure that the dial gauge is securely mounted on a rigid stand or fixture. The stand should be heavy enough to prevent it from tipping over and stable enough to minimize vibrations. If possible, use a magnetic base to attach the stand to a solid metal surface. This provides a stable and vibration-free platform for your measurements.
Pay attention to the orientation of the dial gauge relative to the object being measured. The plunger of the gauge should be perpendicular to the surface to ensure accurate readings. Any misalignment can introduce cosine errors, which can skew your measurements. Visual inspection and careful positioning are key to minimizing these errors.
Remember that external factors can influence the stability of your setup. Air currents, nearby machinery, and even the temperature of the environment can affect the accuracy of your measurements. Try to minimize these influences by working in a controlled environment and taking precautions to isolate the dial gauge from external disturbances. A stable and well-mounted dial gauge is the foundation for accurate and reliable measurements.
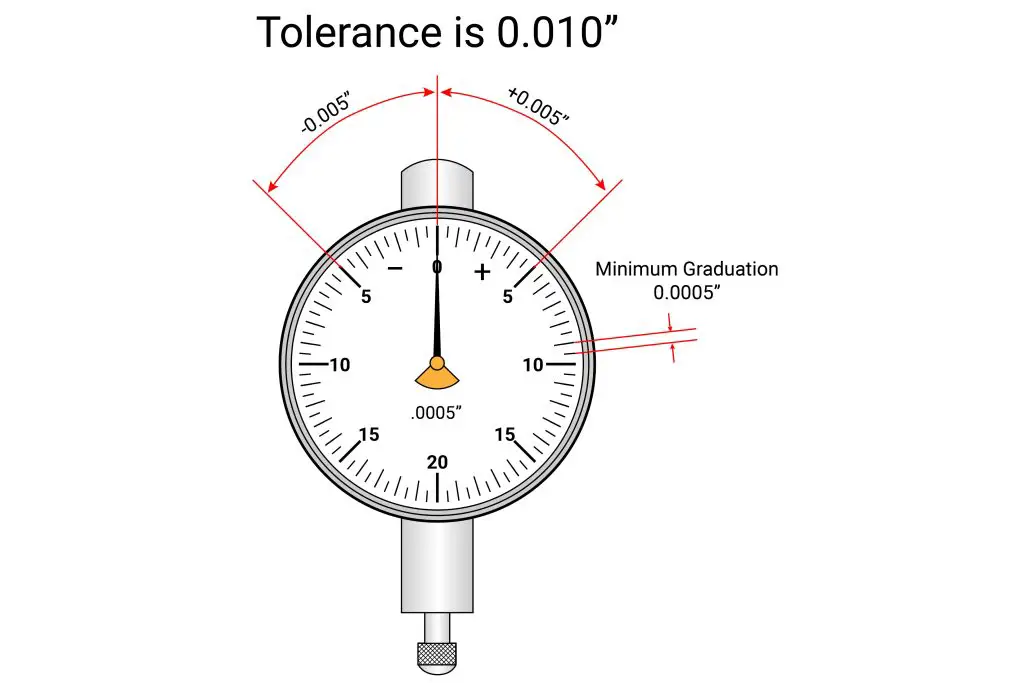
